Principles and Practices for Accurate Thermocouple Measurement with the Q.series X A104.
Introduction to measuring temperature with a thermocouple
Thermocouples operate based on the phenomenon that the junction between two dissimilar metals generates a thermoelectric voltage, a phenomenon known as the Seebeck effect, which increases with temperature.
While virtually any two types of metals can be utilized to construct a thermocouple, specific standard types are commonly employed (refer to Appendix I) due to their predictable output voltages and significant temperature gradients.
Standardized tables provide information on the voltage generated by thermocouples at different temperatures. For instance, a K-type thermocouple, the most widely used, will produce 12.2 mV at 300 °C. This voltage generation means that thermocouples, in contrast to RTDs and thermistors, are self-powered and do not require an excitation current.
Directly connecting a voltmeter to the thermocouple for voltage measurement is not feasible, as it introduces an undesired second thermocouple junction. To ensure accurate measurements, a technique known as cold junction compensation (CJC) is employed. Standard thermocouple tables account for this second junction by assuming it is maintained at precisely 0 °C. Typically, the temperature of the cold junction is sensed by a precision thermistor in close thermal contact with the input connectors of the measuring instrument. The measured temperature from this second thermistor, in conjunction with the reading from the thermocouple itself, is utilized by the measuring instrument to calculate the true temperature at the thermocouple tip.
Q.series X A104 thermocouple module
The Q.series X A104 stands as Gantner Instruments' premier module designed for temperature measurement using thermocouples. The module has the following specifications:
- 8 input channels, each sampling at a rate of 100 S/s
- Compatible with Type B / E / J / K / L / N / R / S / T / U thermocouples
- Margin of error: ±10 µV
- Impressive resolution of 10 nV
- Equipped with a 60/50 Hz noise reduction filter (10 or 6 Hz sampling rate)
- Capable of detecting issues such as broken wires, loose connections, or thermocouple burnout
- Features a channel-to-channel isolation voltage of 100 VDC
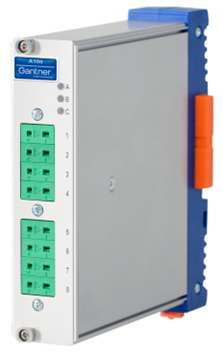
Q.series X A104 TCK
Thermocouple measurement accuracy
While thermocouples are generally reliable for temperature measurements, errors can arise due to several factors. The total error in a thermocouple measurement is the cumulative result of the following components:
- Error originating from the thermocouple itself.
- Error introduced by the extension wire.
- Cold junction compensation (CJC) error.
- Sensor linearization error.
- Amplifier accuracy.
Error in the thermocouple itself
As alloy percentages may slightly vary during each manufacturing process, a small margin of error in thermocouple accuracy is inevitable. Standard thermocouples typically achieve accuracy within approximately 1% of the actual temperature at the measuring junction.
Error in the extension wire
Thermocouples use thin wires to minimize thermal shunting and enhance response times. However, the thin wire introduces a high resistance that may lead to errors, particularly about the input impedance of the measuring instrument. A typical thermocouple with a 0.25 mm diameter (32 AWG) exhibits a resistance of approximately 15 Ω/m. When dealing with thermocouples featuring thin leads or extended cables, it is advisable to keep the thermocouple leads short and employ thermocouple extension wire - characterized by greater thickness and lower resistance - to bridge the gap between the thermocouple and the measuring instrument. Over time, errors may escalate as the wire becomes contaminated from the atmosphere or is exposed to temperatures beyond its tolerance range.
Cold junction compensation (CJC) error
Cold junction compensation addresses the absence of thermoelectric voltage caused by the fact that the thermocouple's cold end at the instrument is not at 0 °C. This compensation enables the measuring instrument to apply established thermoelectric voltage tables (or polynomials) for calculating the temperature at the hot end.
In the Q.series X A104, a Pt1000 sensor is employed to measure the temperature at the thermocouple's cold end. The error associated with cold junction compensation is minimal, measuring less than 0.3 °C.
Sensor linearization error
The thermoelectric voltage of a thermocouple does not exhibit a linear relationship with temperature. The linearity error, exceeding 1% for commonly used thermocouples, becomes even more pronounced below zero degrees. Correcting for this non-linearity is essential for practically every application involving a thermocouple.
The Q.series X A104 incorporates the capability to compensate for the linearity error through the utilization of a look-up table containing voltage-versus-temperature data. The temperature is determined by identifying the two closest voltage readings and then calculating a straight-line approximation between them to derive the temperature. This linearization process is based on a pre-programmed sensor database, offering 300 points for linearization in accordance with EN 60584 standards.
Example 1
In the case of using a type K thermocouple with a maximum measurement range of -200 °C to 1372 °C, the best-fit linearization line is established using 32 points from the look-up table. The maximum linearization error is approximately ±0.4 °C.
Best-fit linearization line (Type K, -200 °C to 1372 °C)
Linearization error (Type K, -200 °C to 1372 °C)
Example 2
Typically, the measurement range can be confined to the practical use case, such as -50 °C to 500 °C. In this scenario, the optimal linearization line yields a maximum linearization error of approximately ±0.03 °C.
Best-fit linearization line (Type K, -50 °C to 500 °C)
Linearization error (Type K, -50 °C to 500 °C)
Amplifier accuracy
The Q.series X A104 modules have a maximum amplifier error of 10 µV. Using a thermocouple type K with an average sensitivity of 41 µV/K, the resulting error is approximately 0.25 °C.
In addition, ambient temperature influences the amplifier error as follows:
- Offset drift better than 1 µV / 10 K, equivalent to a maximum of 0.02 °C / 10 K.
- Gain drift better than 0.005% / 10 K, equivalent to a maximum of 0.1 °C / 10 K at full scale for type K.
Calculating the measurement uncertainty of the Q.series X A104
Without factoring in the thermocouple and extension wire errors, the measurement uncertainty can be calculated. In the example below, we assume a type K thermocouple with a measurement range of -50 °C to 500 °C and the Q.series X A104 module operating at a constant room temperature:
In the case of a +20 °C change in ambient temperature, the error is calculated as follows:
Appendix I
Thermocouple |
Overall range |
Typical accuracy* |
Comments |
Type B (Platinum / Rhodium) |
100 °C to 1820 °C |
5 °C |
Suited for high-temperature measurements. Unusually, type B thermocouples give the same output at 0 °C and 42 °C. This makes them useless below 50 °C. |
Type E (Chromel / Constantan) |
-270 °C to 1000 °C |
1.7 °C |
Type E has a high output (68 µV/°C) which makes it well suited to low-temperature (cryogenic) use. Another property is that it is non-magnetic. |
Type J (Iron / Constantan) |
-100 °C to 1000 °C |
2.2 °C |
The limited range makes type J less popular than type K. J types should not be used above 760°C as an abrupt magnetic transformation will cause permanent de-calibration. |
Type K (Chromel / Alumel) |
-270 °C to 1372 °C |
2.2 °C |
Type K is the ‘general purpose’ thermocouple. It is low-cost and popular. Sensitivity is approx. 41 µV/°C. Use type K unless you have a good reason not to. |
Type N (Nicrosil / Nisil) |
-270 °C to 1300 °C |
2.2 °C |
High stability and resistance to high-temperature oxidation make type N suitable for high-temperature measurements without the cost of platinum (B, R, S) types. Designed to be an 'improved' type K, it is becoming increasingly popular. |
Type R (Platinum / Rhodium) |
-50 °C to 1760 °C |
1.5 °C |
Suited for high-temperature measurements up to 1600 °C. Low sensitivity (10 µV/°C) and high cost make them unsuitable for general-purpose use. |
Type S (Platinum / Rhodium) |
-50 °C to 1768 °C |
1.5 °C |
Suited for high-temperature measurements up to 1600 °C. Low sensitivity (10 µV/°C) and high cost make them unsuitable for general-purpose use. Due to its high stability type S is used as the standard of calibration for the melting point of gold (1064.43 °C). |
Type T (Copper / Constantan) |
-270 °C to 400 °C |
1 °C |
The best accuracy of common thermocouples i, often used for food monitoring and environmental applications. |
* Accuracy at 0 °C unless indicated. Many manufacturers offer special thermocouples with improved accuracy, reaching as low as 0.5 °C.